Manufacturing processes have come a long way since their inception, but the industry-wide challenges have largely stayed the same.
There’s the perpetual search for greater efficiency, the delicate balance between safety and productivity, and the inevitable downtime that brings your operations to a grinding halt. You’ve spent countless hours troubleshooting complex assembly processes and searching for that elusive inventory item in a vast warehouse. It’s a story as old as the manufacturing industry itself.
But what if there was a way to tackle these pain points head-on? A technology that could streamline the way we approach manufacturing, enhancing our operations and empowering our workforce like never before? Enter augmented reality (AR) — a game-changing innovation with the potential to transform the manufacturing landscape and offer solutions to these age-old challenges.
Benefits of Implementing Augmented Reality in Manufacturing
AR brings products to life — and not just for fun and games. From boosting efficiency to elevating safety, it’s redefining how manufacturers approach day-to-day tasks, leading to a more productive and resilient manufacturing process. Some of these manufacturing-specific benefits include:
Improved Accuracy & Precision
With AR, workers receive real-time visual guidance that overlays on top of the physical environment, reducing errors and ensuring higher-quality output. For example, AR can display an image of a correctly assembled product alongside the real product, allowing workers to compare the two and ensure that all components are properly aligned.
Enhanced Safety
AR provides crucial safety information and alerts, minimizing the risk of accidents and creating a safer work environment. Whether that’s highlighting hazardous areas or providing warnings about nearby machinery, AR is helping workers avoid accidents.
Increased Efficiency & Productivity
By streamlining processes and offering instant access to information, AR boosts overall efficiency and productivity. At a basic level, this could mean displaying the optimal path for workers to take when collecting materials, reducing the time and effort required to complete tasks.
Reduced Downtime
Quick access to troubleshooting data and maintenance guides helps minimize downtime and keeps operations running smoothly. AR can help workers diagnose and fix issues quickly, preventing prolonged downtime and costly delays. By displaying a 3D model next to the real thing, workers can identify and replace faulty components more efficiently.
Improved Training & Retention
AR offers immersive, interactive training experiences, accelerating learning and improving knowledge retention. Workers can use AR to practice complex procedures or interact with virtual models of equipment, allowing them to gain hands-on experience in a safe environment. That could mean simulating emergency scenarios, allowing workers to practice their response in a realistic setting.
Augmented Reality Applications in Manufacturing
The manufacturing industry has always been at the forefront of innovation and technological advancement. Since the Industrial Revolution, it’s been the vital engine driving growth and inspiring possibilities. But with the emergence of AR technology, manufacturers can now take their operations to the next level. From streamlining and enhancing quality assurance processes to completely revolutionizing how products are designed, assembled, and maintained, AR has the potential to solve age-old and day-to-day challenges alike.
Quality Control and Inspection
Equipped with AR, workers can overlay digital information onto physical objects, enabling them to quickly identify defects and inconsistencies in products. This does more than streamline the inspection process — it also reduces the risk of human error.
Taqtile‘s mobile AR platform eases quality inspections by enabling employees to access work instructions and related data points using their mobile devices. The AR system highlights the areas that require inspection and displays relevant data points in real-time for thorough and accurate inspections. To go even further, workers can capture images and videos of the inspection process and submit them for review.
And with real-time guidance powered by AR, highlighting areas that require inspection and displaying relevant data, workers generally perform quicker but more thorough inspections. As an added perk, it also empowers remote expert assistance, where offsite experts can view the situation through the worker’s AR device and provide guidance to resolve issues without the usual back-and-forth.
Like GE and Volkswagen, the German engineering and technology company, Bosch, has been using AR technology to support its quality control processes in its automotive division.
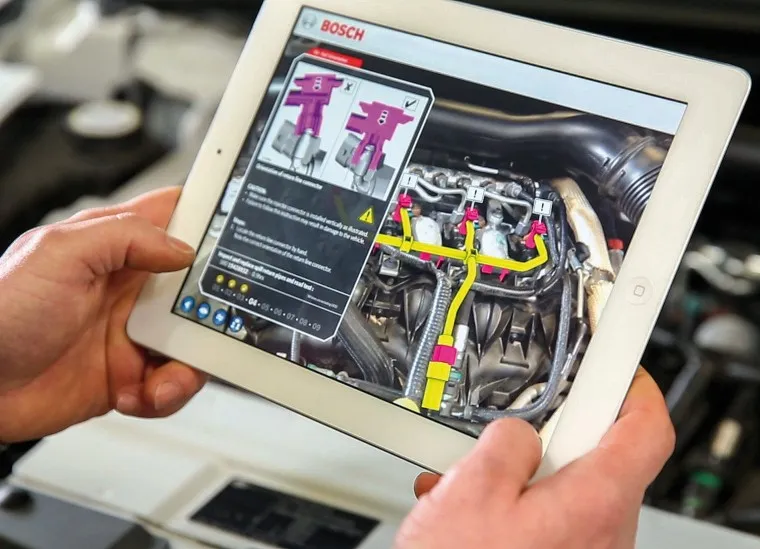
When workers encounter an issue during control processes, they can use smart glasses to connect with remote experts who can view the situation through AR and troubleshoot how to resolve the issue immediately.
Design, Assembly, and Maintenance
With virtual prototypes of products overlayed on tangible workspaces, designers can see how their products will look and function in the real world. This speeds up the design process and enables designers to identify and resolve issues early on, reducing the risk of costly errors and delays. With AR, designers can make changes in real-time, seeing how they will affect the final product before committing to them.
McLaren, the British sports car manufacturer, has been using AR technology to create 3D virtual models of cars and view them in a real-world environment. By visualizing their designs before they’re actually produced, they open the door to collaboration between designers and engineers.
With open communication like this, their teams work together to create the best possible designs that are as aesthetically pleasing as they are functional and safe.
Once the product reaches the assembly stage, AR provides workers with real-time guidance and support. Similar to its use in QA and inspection, AR glasses can display digital work instructions over the physical parts, leading to significant improvements in efficiency and accuracy, as workers are guided through the assembly process step-by-step. The use of AR technology in assembly can also help reduce the need for physical clamps and workpieces, saving time and resources.
AR technology has even helped companies like Volvo improve the accuracy and efficiency of their assembly tasks. Engine quality control and assurance in Volvo’s manufacturing plants are subject to rigorous quality checks; each engine requires 40 checks, with 200 possible quality assurance (QA) variants, all of which must be completed at the QA station in only eight minutes.
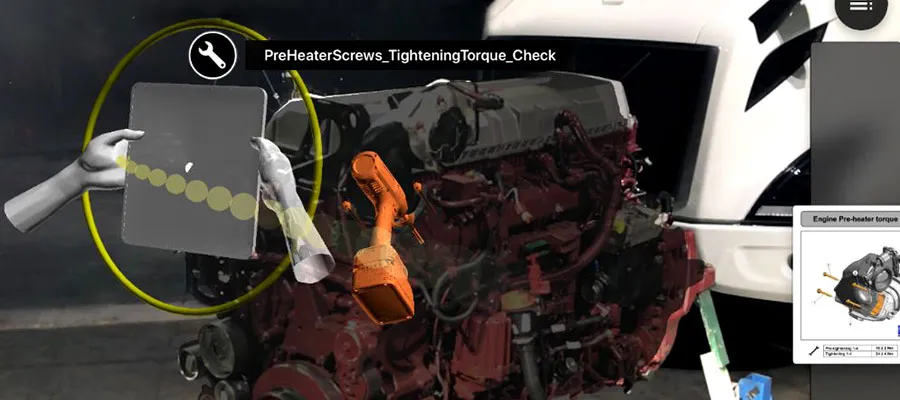
Because it’s enabled workers to perform their tasks with more precision and confidence, they’re seeing sustainable jumps in productivity, quality control, and process efficiency.
Finally, once the assembly is complete and deployed in the field, AR can be used to maintain that product by providing workers with real-time information about exactly what they’re servicing. AR glasses can display digital overlays of maintenance procedures and provide access to equipment manuals, reducing the risk of errors and ensuring that maintenance tasks are performed correctly and safely. And what’s better than equipment uptime and reduced maintenance costs?
Inventory Management
When it comes to managing inventory, an eye for detail is everything. And anything that can be done to make it less reliant on human error is a game-changer.
Luckily, AR is making waves by providing workers with real-time information about inventory levels and locations. With AR-powered glasses, workers can view digital overlays of inventory information in physical spaces, allowing them to quickly identify and locate items.
In fact, Boeing is putting AR to work for its aviation division. The company’s technicians use smart glasses to view real-time inventory information, reducing the time needed to locate parts and improving overall efficiency.
Similarly, it can be used to speed up the process of inventory tracking and auditing. Workers can quickly scan barcodes or QR codes on inventory items and instantly access relevant information (i.e. item name, quantity, location, etc). This can help reduce errors and ensure that inventory records are fresh and accurate.
Coca-Cola is using AR technology in its bottling plants for exactly that. With AR glasses, workers can quickly scan barcodes on inventory items, identifying and locating inventory items in a snap. By reducing the time needed to complete production tasks, they also reduce the time and resources needed to produce Coca-Cola products.
And — like with inspection or assembly — AR can be used to provide workers with real-time guidance and support during inventory tasks. With AR glasses, workers can view digital work instructions overlaid onto the physical inventory items, ensuring that they are handling items correctly and efficiently. This can lead to significant improvements in efficiency and accuracy, as workers are guided through the inventory process step-by-step.
Equipment Operation
AR technology provides workers with real-time information, guidance, and support in more ways than one. For basic, day-to-day operations, AR can overlay digital work instructions onto physical equipment, ensuring that operators are using the equipment correctly and efficiently.
It can also continuously display digital overlays of equipment information (i.e. performance data and maintenance schedules). Workers can monitor each piece of equipment, so they can quickly identify and diagnose issues when they arise.
Siemens has taken this use case to heart. Recently, they developed a “smart” helmet equipped with AR technology. The helmet has a transparent visor that can display digital overlays of work instructions and performance data, allowing workers to quickly access the information they need without having to look away from the equipment they are operating.
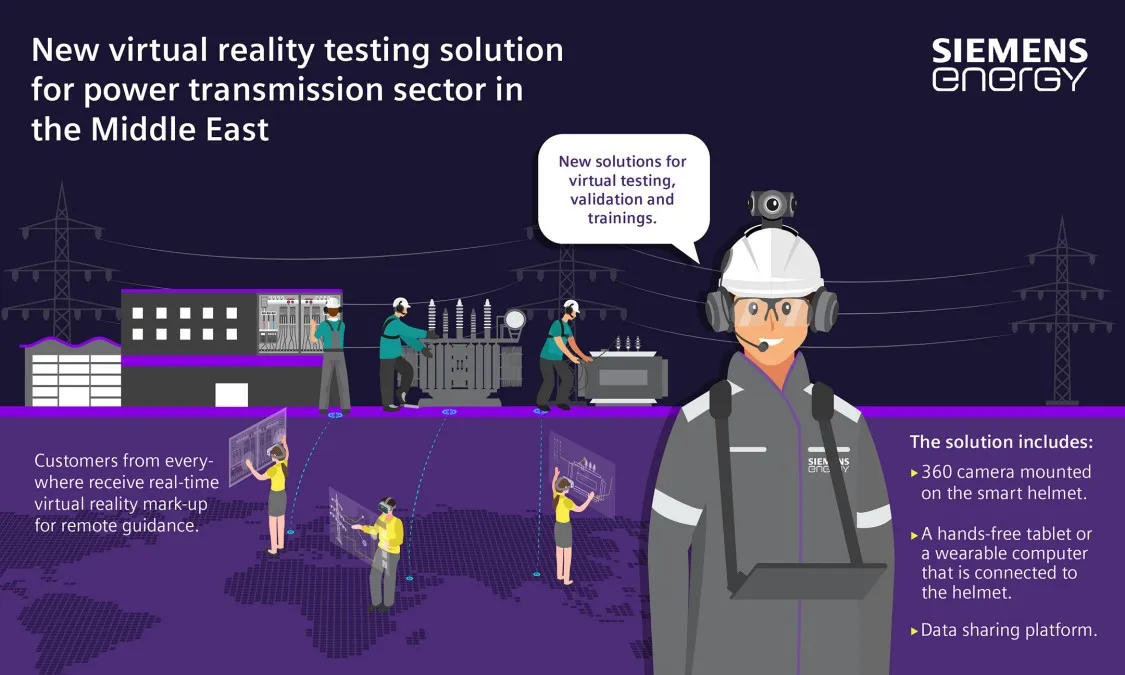
And when problems get extra tricky — which, of course, they tend to do in manufacturing — AR glasses can offer real-time remote support from experts, enabling workers to access guidance and support from anywhere in the world.
So, instead of waiting for the vendor to call you back when your machines are down, consider an alternative suggested by Scott Burkey, technology fellow at WestRock: What if you could use a device, get on an instant call with your vendor, and save yourselves 90% of the looming downtime? With AR, you can — and WestRock is experiencing these downtime savings firsthand.
Training and Simulation
What if you could provide your workers with hands-on training and real-world experience in a safe and controlled environment? Now, you can.
With AR glasses or mobile devices, techs can view digital overlays of training materials and simulations on top of physical equipment or in their workspaces.
As an added bonus, according to Koch Industries, AR reduces time to manufacturing training proficiency by 50-70%. And if you can turn a six-month training session into several weeks, you’re putting that allocated resource to use long before they were expected.
Better yet, AR technology also offers workers the ability to practice and learn skills in a virtual environment, boosting their confidence and proficiency before working with physical equipment. When techs are confident and proficient in their tasks, they reduce errors and minimize the risk of accidents during training and day-to-day work.
PBC Linear, for instance, launched an AR-based training program to train employees on the assembly and disassembly of linear motion systems, including linear bearings, rails, and actuators. With the help of AR, their employees learn the correct procedures for assembling and disassembling these systems, as well as how to troubleshoot issues and perform maintenance tasks.
AR technology can provide workers with real-time feedback during training and simulation activities, helping them tweak their approaches and improve their skills more quickly. After all, little steps amount to significant improvements in efficiency and accuracy in the long run. And in the manufacturing industry, that means cost savings and improved productivity.
Challenges of Implementing Augmented Reality in Manufacturing
Needless to say, AR has enormous potential to transform the manufacturing industry, offering solutions to both long-standing challenges and day-to-day operations. But of course, nothing revolutionary goes without at least some integration challenges. These are some of the common ones manufacturers face when implementing AR in their operations:
Cost
Integrating AR into existing systems can be a challenge due to the significant upfront hardware and software investment. Prepare for costs associated with purchasing AR devices, creating and/or buying AR content, and integrating AR with existing systems. Plus, factor in any training costs that you may need for workers to effectively use AR technology. And, if you plan to go with a traditional mobile device manager (MDM), account for ongoing attention with regard to device management, software updates, and providing user support.
Training & Skills
Training programs need to cover a variety of topics depending on the specific AR technology being implemented. That may include training on how to use AR devices and software, how to navigate augmented reality interfaces, and how to interpret and act on real-time data displayed through AR. Plus, workers may need to learn new safety protocols and procedures, as AR — though generally safe — can introduce new safety risks and hazards. Essentially, plan for training programs that are comprehensive and tailored to the specific needs of your organization and workforce.
Compatibility & Integration
Integrating AR with existing systems can present compatibility challenges. For example, if the AR system requires high-performance hardware, it may not be compatible with older hardware systems. Or if the AR system requires specific software or operating systems, it may not be compatible with existing software or systems. Compatibility challenges can also arise when integrating AR with other technologies, such as robotic systems or older machinery. Carefully consider each of these compatibility challenges and plan accordingly.
Security & Privacy Concerns
Ensuring the security of sensitive data and protecting user privacy are critical aspects of AR implementation. Proper security protocols and measures must be put in place to prevent breaches. Depending on your organization, that might include limiting access to authorized personnel, encrypting data transmission, storing sensitive data securely, conducting regular security audits, and training employees to recognize and respond to potential security threats. You’ll want to take every measure to ensure the security of data and protect your organization’s privacy.
User Adoption
Convincing veteran manufacturers and less tech-savvy individuals to embrace AR technology can be challenging. There might be a lot of initial apprehension toward any immersive tech. But with clear communication and training programs, you can slowly introduce them to the idea to ensure that all users are comfortable and confident in using AR devices.
Device Management
Existing device management solutions for companies using AR won't work in manufacturing settings. Managing multiple AR devices in manufacturing operations is challenging. Manufacturers have to perform regular updates to keep everything compatible. This can be particularly tricky in large manufacturing settings or where IT isn’t at your beck-and-call, so you’ll need a dedicated solution for XR devices.
Final Thoughts
The future of AR in manufacturing is bright despite the presence of a few hurdles. Fortunately, innovative companies like ArborXR are addressing these challenges with dedicated XR MDM solutions, designed specifically for manufacturing.
As AR technology continues to evolve, we will undoubtedly see the existing AR challenges morph and shift alongside more powerful and versatile applications in manufacturing. Increased adoption rates will lead to greater integration and innovation across the industry, ultimately driving increased efficiency, productivity, and competitiveness.
The addition of devices like the Meta Quest Pro will only increase AR’s adoption. By providing a vehicle for seamless switching between AR, VR, and the physical world, this advent of mixed reality will further accelerate its applications in manufacturing and beyond.
Ultimately, the integration of AR technology in manufacturing processes has the potential to improve efficiency, reduce errors, and increase productivity, resulting in cost savings and a competitive advantage in the manufacturing industry.
Are you ready to explore the use of AR in your manufacturing operations? Give us a shout or get started today.