Warehouse environments are fast-paced and can be high-risk, yet traditional training relies on trial and error. This outdated approach puts workers at risk and costs businesses money, especially as demand for skilled workers grows.
Today’s warehouses face unprecedented challenges. With surging online orders and high worker turnover, they need to train employees quickly without compromising safety. Virtual reality offers a solution.
In this ArborXR guide, we’ll show you how VR transforms warehouse training and why it’s becoming essential for modern operations.
Understanding VR Warehouse Training
VR warehouse training puts workers in virtual environments where they master critical skills before stepping onto the warehouse floor. Through VR headsets and motion sensors, employees navigate detailed replicas of their future workspaces, repeating complex tasks until they achieve mastery.
Common training applications include:
- Lockout/Tagout (LOTO) Procedures: Workers power down and secure automated equipment, practicing the precise steps that prevent accidents during maintenance.
- Pallet Management: Employees stack and arrange pallets to maximize space while maintaining stability, developing muscle memory for safe, efficient storage operations.
- Forklift Operations: Operators maneuver through challenging scenarios, learning to handle loads and navigate tight spaces without risking equipment damage or injury.
- Order Fulfillment: Teams use tools like RF scanners and audio systems to locate, pick, and process orders accurately, building speed without sacrificing precision.
- Truck Loading: Personnel optimize cargo space and practice proper lifting techniques, preventing injuries while maximizing load efficiency.
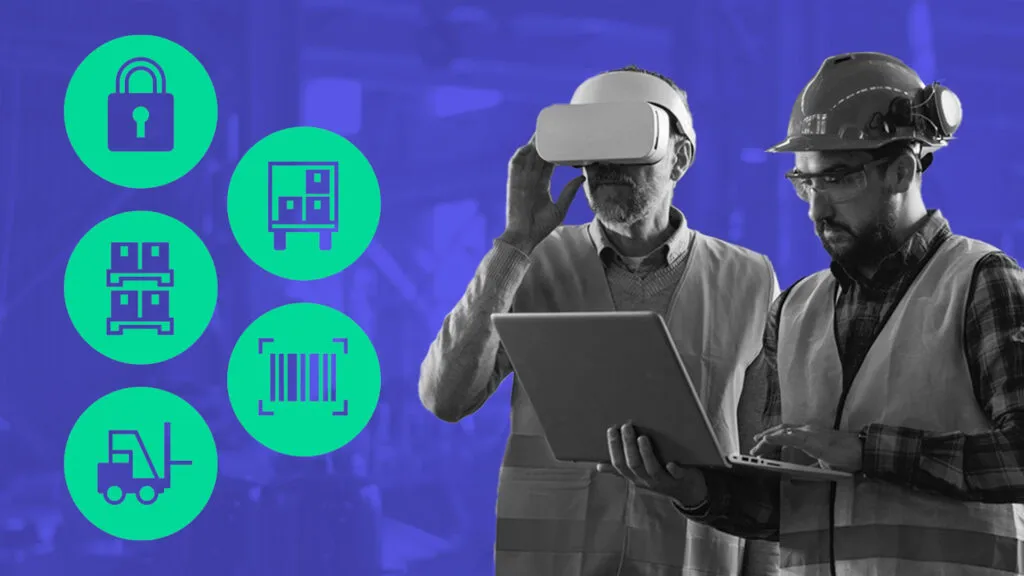
Benefits of Warehouse VR Training
Better Learning and Retention
The warehouse industry faces a massive challenge—a 49% annual turnover rate, according to the U.S. Bureau of Labor Statistics. With nearly half of warehouse workers leaving their jobs each year, rapid and effective training is critical for maintaining operations.
VR training addresses this challenge by immersing employees in realistic scenarios. Workers can practice tasks like forklift operation and order picking with no risk of accidents or mistakes. The ability to receive instant feedback and repeat tasks builds confidence and improves skill retention.
Safer Training
Warehouses are inherently hazardous environments, but VR creates a safe space for learning. Workers can practice handling emergencies like spills and equipment failures without real-world risks, making sure they’re better prepared for challenges on the warehouse floor.
Superior Beverage is a great example of VR’s impact on safety.
After implementing VR training for complex robotic systems, they cut workplace injuries in half, reduced training costs by 12%, and accelerated new employee productivity by 33%. The safe virtual environment lets workers build confidence and competence before handling actual equipment.
Less Training Time and Expenses
Traditional warehouse training disrupts operations, but VR training allows employees to learn while work continues. This minimizes downtime and maintains productivity. The safe virtual environment also reduces injuries, lowering medical costs and workers’ compensation claims.
A large Distribution Center in Belgium partnered with OneBonsai to capitalize on VR’s efficiency. Their system now trains new warehouse personnel across three shifts, 24/7, reducing the need for physical training facilities.
VR training also cuts costs by replacing expensive equipment and trainer fees with digital simulations that scale. Companies can train large groups simultaneously, accelerating team readiness without exponentially increasing costs.
Examples of VR Training in Warehousing and Logistics
1. Walmart Scales VR Training to Reach Over 1 Million Employees Nationwide
Amazon warehouses process millions of products daily. They’re well-oiled machines that demand speed and precision while maintaining safety.
2. DHL's Package Loading Training
DHL implemented VR training to optimize package loading efficiency across their global operations. The program teaches employees loading techniques through gamified scenarios, where unused space is highlighted and workers compete on an international leaderboard that spans 40+ countries.
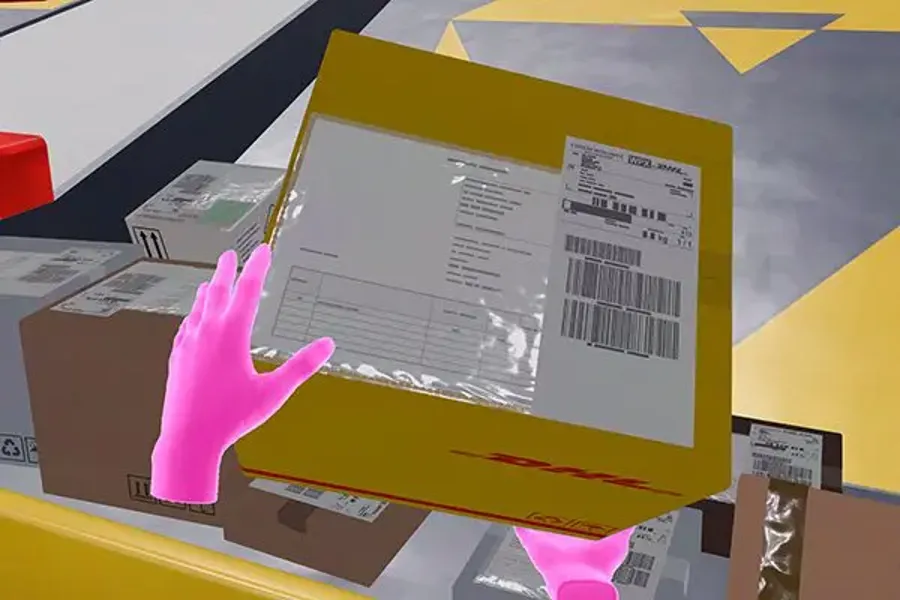
The results have been impressive to say the least—99% of trained employees report improved performance and reduced workload.
How to Get Started with VR Warehouse Training
Implementing VR training requires careful planning and investment in tools and content. While it’s a significant decision, forward-thinking companies recognize the long-term benefits in safety, efficiency, and employee retention.
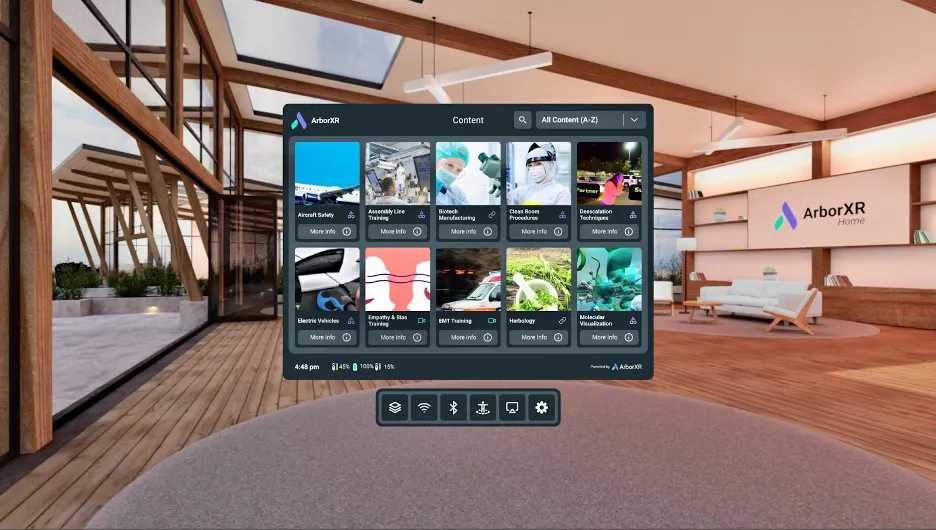
One critical factor in maximizing your VR training program’s potential is the ability to deploy and manage headsets and content at scale. ArborXR’s XR device management solution helps streamline VR training rollouts by offering:
Remote Device Management
Control hundreds or thousands of VR devices across multiple locations. Manage features like brightness settings, WiFi connectivity, data security, and battery monitoring from one central platform.
Content Delivery
Deploy training modules securely, whether from third-party providers or XR developers in our XR directory. The platform includes Kiosk Mode to restrict devices to specific training apps, ensuring focused learning sessions.
Companies like Walmart and Smooth Soft have seen great results with VR. Walmart implemented VR training in 5,000 stores with ArborXR and helped employees retain information 70% better than traditional methods, leading to faster onboarding and smoother operations at scale.
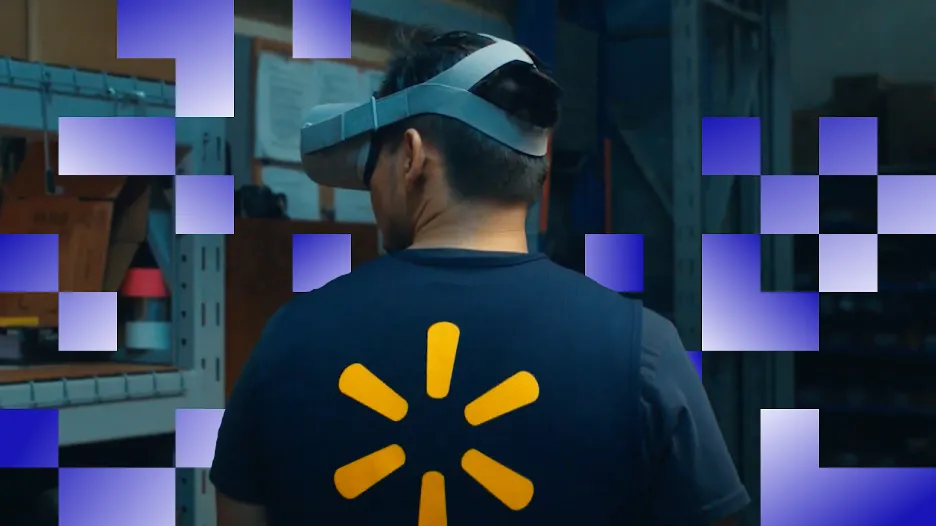
Additionally, Smooth Soft used ArborXR to train restaurant employees in customer service and operations. Training time was cut in half, and costs were significantly reduced, with employees gaining hands-on experience in a safe environment, improving efficiency and job performance.
Embrace the Future of Warehouse Training
VR training is transforming how businesses prepare employees for high-stakes warehouse environments. It offers safer, faster, and more effective learning that reduces costs while improving performance.
As worker turnover remains high and safety demands increase, VR provides a practical solution for rapid, thorough training. With tools like ArborXR, companies can scale their VR programs efficiently and prepare their workforce for success.
Ready to modernize your warehouse training? Partner with ArborXR today and unlock the full potential of immersive learning.